You may have seen us at the World Electrolyser Congress 2025 with a model of an unusual looking electrolyser stack. There are two reasons for its appearance. First, to lower the levelised cost of production (LCP) it operates at high pressure, which we’ve discussed here. It’s also designed to minimise development risk and enable low-cost manufacturing, which we explain below.
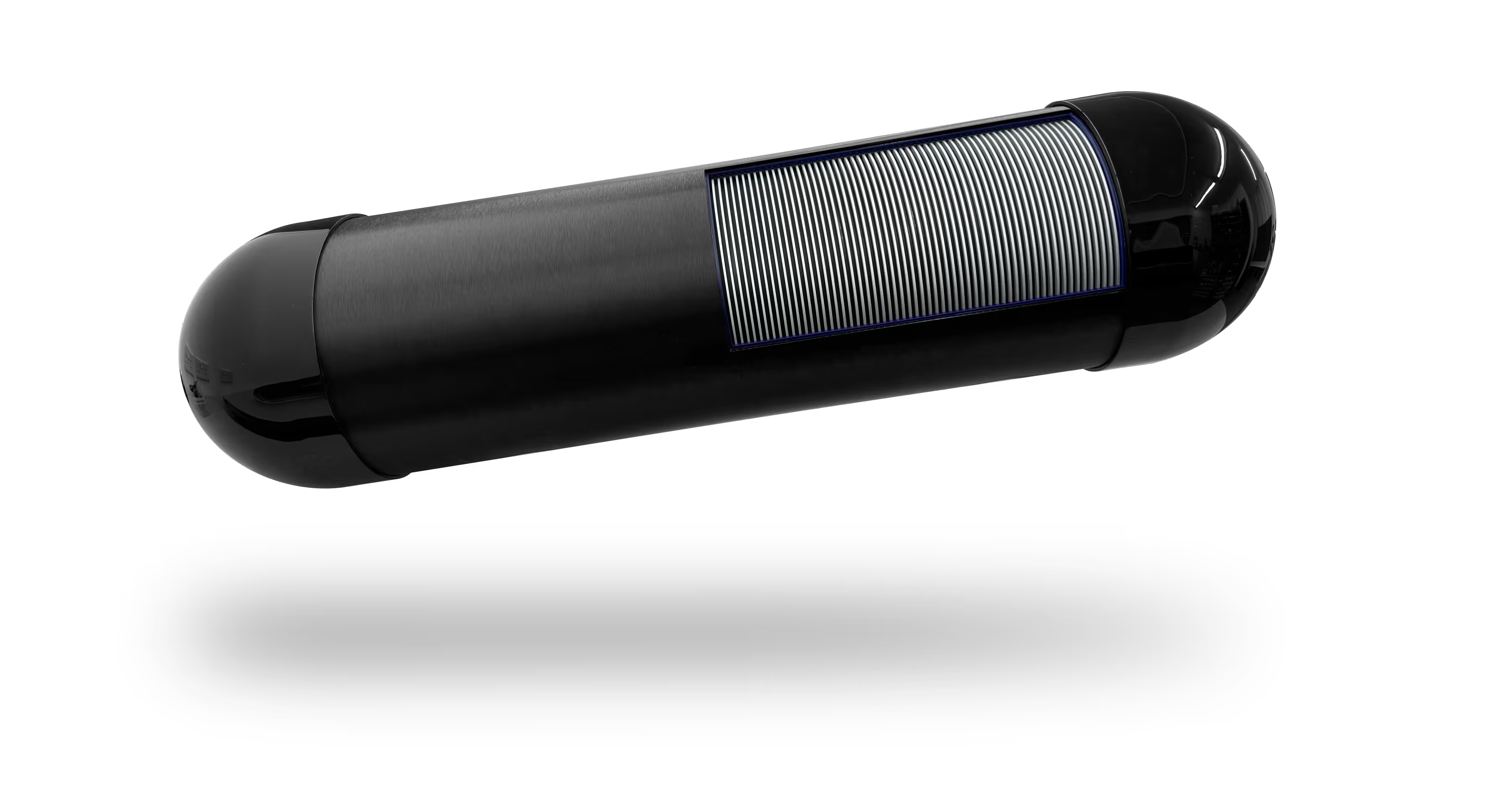
Accelerating the adoption of electrolysers
Three hurdles (at least) stand in the way of the commercialisation of novel electrolyser technologies.
The first of these is development risk. Solutions need to be highly dependable by minimising fundamental development challenges.
The second is the levelised cost of production – LCP – in order to compete with traditional ways of making base chemicals. The part of LCP that is very directly in our gift as technology developers is CAPEX, the cost of the equipment.
Finally, production needs to be easy to ramp, so it can grow from a relatively small initial volume without under-utilisation of factory capital.
Our electrolyser design responds to all of these pressures.
Our solution
We’ve addressed development risk by deliberately using production-intent cells of the same scale as early development prototypes. This reduces development time and risk by avoiding the need to reconsider thermal design and flow management as cell size is increased during technology development.
To address the CAPEX barrier, all the cell components in our system are designed for low-cost manufacturing and assembly.
They can be made using low-cost processes such as injection moulding; they are designed to be suitable for machine sorting and orientation, picking, and placement during assembly; and they’re of a similar scale as the parts of fast-moving consumer goods (FMCG), such as personal care products, food packaging or medical consumables.
This means that electrolyser stacks could be automatically assembled by adapting machines designed for FMCG, without the need to develop dedicated automation equipment from scratch.
Making use of existing automation solutions for handling components of everyday products also reduces factory footprint and the associated set-up timescales, technical risk and cost.
This means that factory capacity for our electrolyser technology can be established and expanded in lockstep with demand.
Bigger isn’t always better
Our shortcut to a proven solution and lower LCP has resulted in an electrolyser stack that looks radically different to the norm. Most obviously, it’s much smaller than the norm.
In a recent whitepaper, we’ve shown that “bigger isn’t always better” anyway when it comes to electrolyser cell size and optimising for LCP. In particular, we considered green hydrogen and the levelised cost of hydrogen (LCOH) that can be achieved with alkaline water electrolysis (AWE), proton exchange membrane (PEM), and anion exchange membrane (AEM) technology.
Compatible with other innovations to reduce cost
Our design also opens up other potential advantages. It uses AEM chemistry, making it efficient for green hydrogen generation from variable renewable power.
The stack is also designed so it can be built into a pressure vessel. We expect that pressurised production will reduce the costs associated with hydrogen compression for transport and downstream uses. Because the stack is small, the wall thickness of the vessel can be kept low, because hoop and longitudinal stresses are lower than they would be at a larger scale for comparable pressures.
In fact, the size of our stack means that the pressure-resistant container is of a similar size to a typical type 4 hydrogen container for a fuel cell electric vehicle. Leaning on this existing solution from another industry could further reduce manufacturing cost, risk, lead time and set-up cost.
Several aspects of our electrolyser design for low-cost manufacturing and assembly are protected through patent applications, ready for further development and commercialisation with a partner looking to unlock the unique advantages of AEM technology.