Green hydrogen is the best chance we have at replacing oil and gas in hard-to-electrify transport and industrial applications. But while the oil and gas industry has long benefitted from abundant fossil fuels, hydrogen doesn’t have this luxury. What’s more, green hydrogen requires sophisticated technology and renewable energy for its production. Yet, it needs to go from outsider to mainstream energy vector in a decade, if we are to build a net-zero world.
That means we need to rapidly scale up green hydrogen production. Fortunately, the tools to make hydrogen, i.e., electrolysers – electricity-powered devices that split water into hydrogen (H2) and oxygen (O2) – are a rapidly advancing technology. Membrane-based electrolysers (proton-exchange membrane, PEM, and anion-exchange membrane, AEM) are likely candidates for mass adoption as they do not require a continuous power supply, making them ideal when working alongside intermittent renewables.
A number of manufacturers have efficient designs for both types, as well as alkaline water electrolysers, that are commercially available or in development. But there are reports of rapidly growing order books – or “backlogs” – at electrolyser makers, throwing into doubt our ability to soon produce at the scale needed to create a zero-carbon economy.
These companies – and others embarking on new electrolyser designs – need to find ways to produce them quickly, cheaply and at scale, following in the footsteps of solar panels and batteries. To think about how we do this, we first need to consider the scale of the challenge we face.
The scale of the challenge of making green hydrogen
Industry and governments now are forming partnerships where vast numbers of electrolyser stacks – probably in shipping container sized units – will be deployed at large scale renewable energy sites. Using this power, they will turn a flow of water into green hydrogen, which will then be piped or shipped to users. We think it also makes sense for many smaller, distributed operations to be deployed where hydrogen is needed, for example on industrial or refuelling sites (bus stations, airports).
These facilities combined will need to turn 850 gigawatts (GW) of power into hydrogen by 2030, according to the International Energy Agency, to stay within 1.5°C of global warming. That is a big leap.
In 2021, the entire global installed capacity of electrolysers producing green hydrogen rated at 250 megawatts (MW). We need 3,000 times that by 2030.
In terms of renewables generation, today’s hydrogen electrolysers consume the power of 50 large wind turbines. By 2030, we would require 170,000 of the same turbines for hydrogen production – the equivalent of total global wind generation today. But with vast investment and falling costs around the world, a huge growth in renewable energy seems certain.
Looking at the scale of the challenge in terms of hydrogen produced and transported, we need to scale up from filling one lorry with green hydrogen globally every ten minutes, to five lorries every second.
And to consider the manufacturing and assembly challenge, membrane-based electrolysers will need to go from a membrane area of three football pitches to an area of 20 times the City of London (or about 6750 football pitches).
At a cell area of 1 metre x 1 metre and depth of 10 mm, this translates into 52 million membrane electrode assemblies (MEA) that need to be assembled into 520 km of electrolyser stacks.
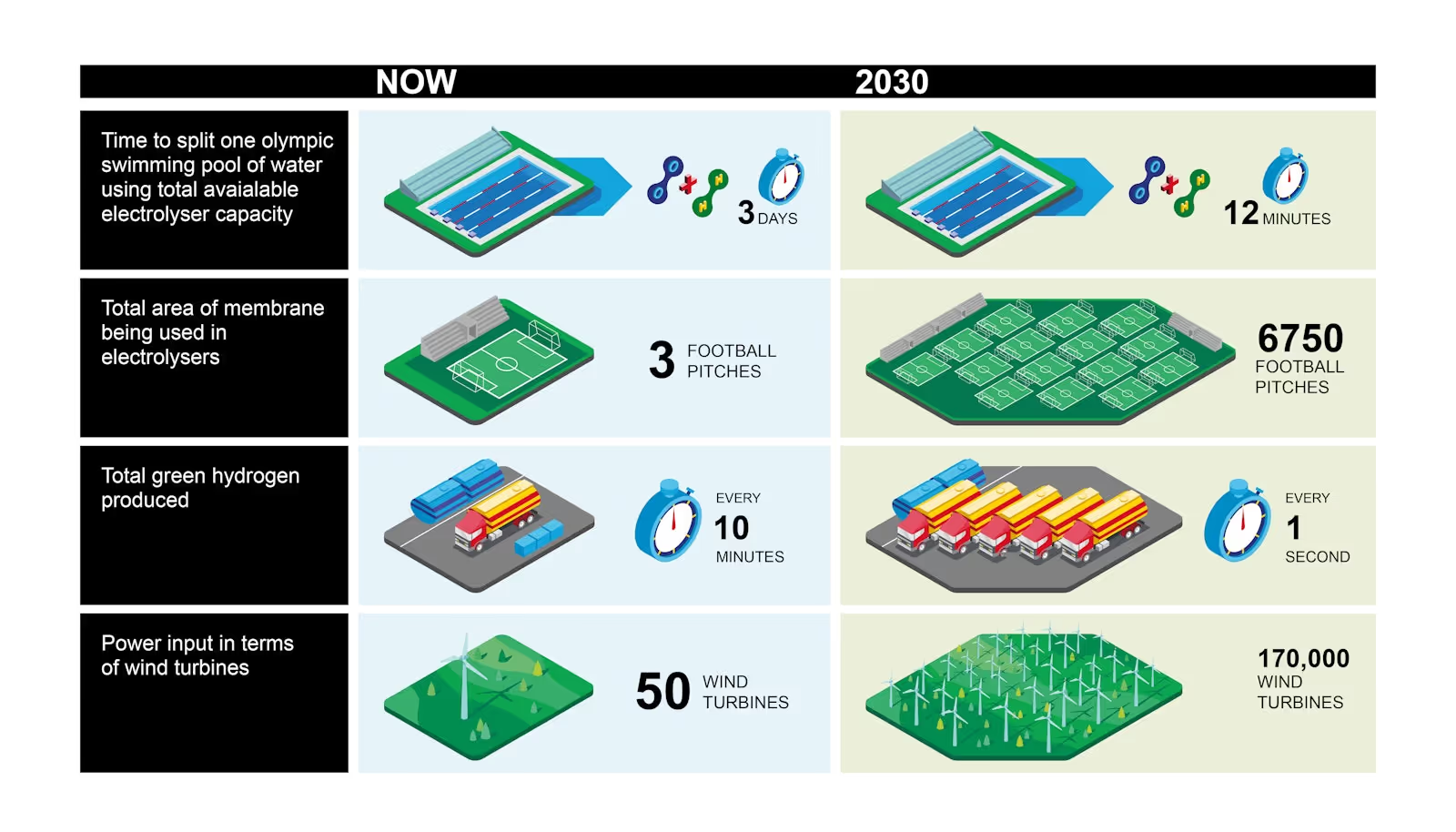
Scaling electrolysers rapidly
One half of that challenge is expanding renewable energy capacity. Less discussed, but just as important, is the other half of the challenge: producing electrolysers at scale.
But that, too, is not unrealistic. Emma Champion of BloombergNEF, recently told The Economist , that by the end of this decade she predicts green hydrogen will be cost-competitive with hydrogen from fossil fuels, thanks to innovation and economies of scale [1]. With smart strategic decisions around investment and manufacturing, electrolysers could fall in cost, just as solar cells and batteries have, making them the next commodity technology that disrupts fossil fuels.
To make this happen, we need to see the total cost of ownership of electrolysers – production and maintenance of electrolysers and cost of electricity – become much lower.
There are promising moves: Siemens has plans to mass produce electrolysers to get the cost down for their hydrogen gigafactory in Berlin, which will be up and running in 2023 [2]. Enapter wants to reduce the cost of its anion-exchange membrane (AEM) machines by 83.5% over the next three years due to economies of scale and automation at its new factory in Germany [3]. Others are making similar moves.
But this is bigger than a few companies. Too many electrolyser designs are too complicated to rapidly scale. Mass production needs to become widespread quickly.
The fastest way to do that is to design electrolysers that can be made easily, using readily available materials and existing infrastructure. Some of this may mean small tweaks to components. Others may mean changing fundamental design decisions.
The lessons from today’s winners
This approach has some impressive precedents. Part of the reason Tesla was able to go from start-up to world’s most valuable automaker in less than 20 years was an early decision to use cylindrical cells (which look like AA batteries). These were easier to make than its competitors’ bespoke battery designs and could be produced by relying on existing battery manufacturing infrastructure [4].
That meant it could produce its cars far quicker and more cost-effectively than competitors. It is also part of the reason for its early leap ahead – an advantage it maintains to this day. Electrolysers have an opportunity to deploy the same strategy of cost-effective mass-production to scale rapidly.
In our next blog, we will discuss how to do that.
References
01. Green gases can help in the shift from fossil fuels to electricity, The Economist
02. Siemens Energy to build ‘multi-gigawatt’ hydrogen electrolyser factory in Berlin. Recharge
03. Enapter eyes 83% cost reduction for its unique AEM hydrogen electrolysers by 2025, Recharge