Next-generation lidar sensors require technologies for steering the ranging laser over the scene encountered by the vehicle that meet the cost point OEMs are willing to pay for series production components and are vastly more compact and reliable than the conspicuous mechanical “buckets” that sat on the roof of the first self-driving cars.
A range of solutions to this challenge are currently being developed, all jostling for adoption by OEMs. Building on TTP’s record of developing low-cost sensors for a wide range of industries, we have set ourselves the challenge of designing and building a “perfect” beam-steering unit for next-generation lidar.
How do we define “perfect”?
We want to design a beam steering unit that will easily meet the performance requirements for automotive lidar in terms of range, field of view (FOV) and resolution, is suitable for low-cost manufacture, and is compatible with a wide range of next-generation lidar systems.
Key points in this blog:
Selecting the best beam steering technology
Designing a “perfect” beam steering unit
Our MEMS mirror beam steering units
Technology options for laser illumination
Our first step on this journey was to review and pick the right type of technology from the main contenders.
Flash lidar is a fully solid-state method for measuring the entire field of view without the need for moving parts. A wide-angled flash of laser light illuminates the scene, and spatial information is measured by imaging the reflected laser light on a two-dimensional array of photodetectors – similar to a digital camera but with the crucial difference that distance is measured in addition to position and intensity.
This could be thought of as the most elegant form of beam steering. The illumination light is directed simply by the positioning of emitters and the fixed optics in front of them. Flash lidar is not without its limitations though. The amount of light produced is finite, so decisions must be made about how to spread this out into the scene, i.e., whether you focus it on a small scene in the distance, or whether it is spread out over a wider scene at short range. This is being addressed by increasing the brightness of the lasers, the sensitivity of detectors and the efficiency of optics, but the trade-off between range and field of view remains for now. While these systems will most likely get close to perfect in the future, we need to look at other technologies for now.
Then there are newer optical approaches with the potential to offer an attractive combination of compactness, robustness, and performance. Optically phased arrays (OPAs), for example, use timing delays between an array of emitters to focus the laser power at specific points through interference between adjacent beams.
This has great potential in terms of performance, but the biggest challenges lie in manufacture. Precise control of the interference (i.e., the time delays) is generated by making very subtle changes to the path length of light before it is emitted. Systems which can manipulate light with nanometer precision have so far been confined to research labs because of the size, cost and complexity of the equipment required.
Perhaps the most compelling beam steering systems available at scale right now are MEMS mirrors (where MEMS is short for micro-electromechanical system).
These milli-scale silicon mirrors “wobble” predictably to change the deflection angle of an incident laser, thus steering the ranging laser across the scene. These systems use focused laser beams more like laser pointers, unlike the flash systems, and this makes it easier to achieve a 200m + range.
Unlike flash laser and solid-state optical systems, there are no deep technological barriers to achieving the performance required for automotive lidar, and MEMS mirror units also have no sliding parts that compromise reliability.
Crucially, MEMS mirror beam steering devices are made by traditional silicon layer-by-layer processing techniques and can therefore be as cheap as a few dollars per mirror to manufacture at volume.
However, these are not the principal reasons why we see MEMS mirrors as potentially the “perfect” solution for beam steering.
Beam steering sits at a crucial intersection between lidar sub-systems and the “perfect” mirror therefore looks different depending on the surrounding sub-systems in the lidar sensor. The design of MEMS mirrors is extremely flexible, so as a tailored solution they have a good chance of meeting the long list of requirements.
This presents great potential for optimisation of mirrors, which can translate them into the perfect beam steering unit for a particular lidar system. This alleviates development headaches by removing constraints on other sub-systems.
Designing a beam-steering unit
From the outset, we decided to design for resonant frequency, essentially how fast the mirror “wobbles” back and forth. This determines how quickly you can pulse your laser and the detector framerate. We chose this to be sufficiently high that the mirror is largely immune to vibration from road noise but also low enough that we were confident of achieving a range of sizes and geometries.
Further, we decided to drive the motion of our mirror electromagnetically, similar to an electric motor. This presents advantages as electromagnetic actuation is well suited to controlled, large displacement applications and it can generate position-encoding information for closed-loop control from back-EMF measurement. This is particularly useful for functional safety as the position encoding is intrinsic to the design and doesn’t require additional sensing components.
On account of these preferences, we opted for a torsional beam mirror design, a simple design which works well with an electromagnetic driving scheme.
Then there are trade-offs that can be made in the design. For example, to make life easier for the laser optical design and alignment, you want a larger mirror. By tweaking the mirror in this way, you get better resolution and range from worse performing emitters. However, making the mirror larger then means you must provide a larger, stiffer beam to achieve the same resonant frequency – and this may have consequences for the potential FOV you can get from it.
Other design constraints are presented by limitations of MEMS (micro-electromechanical system) manufacturing methods. Material choices need to be pinned down early, as the electrical and mechanical properties of the materials and layers are very important during the design process. For example, different densities or stiffnesses will immediately change the resonant frequency of the mirror.
So, we knew what overall design we wanted – an electromagnetically driven, torsional beam – and we knew the resonant frequency we would be aiming for. All that left was detailed design of the exact geometry, which would give us the required scanning angles while navigating the trade-offs discussed above.
The detailed design of the device used multiphysics simulations of the electromagnetic forces, solid mechanics and damping to calculate scanning range for a chosen geometry that would translate into the sensor FOV. Larger scan angles for a given resonant frequency being the target performance metric. After multiple design iterations, we have produced a range of designs with mirror diameters ranging from 3 to 5 mm that were prototyped via MEMS processing techniques.
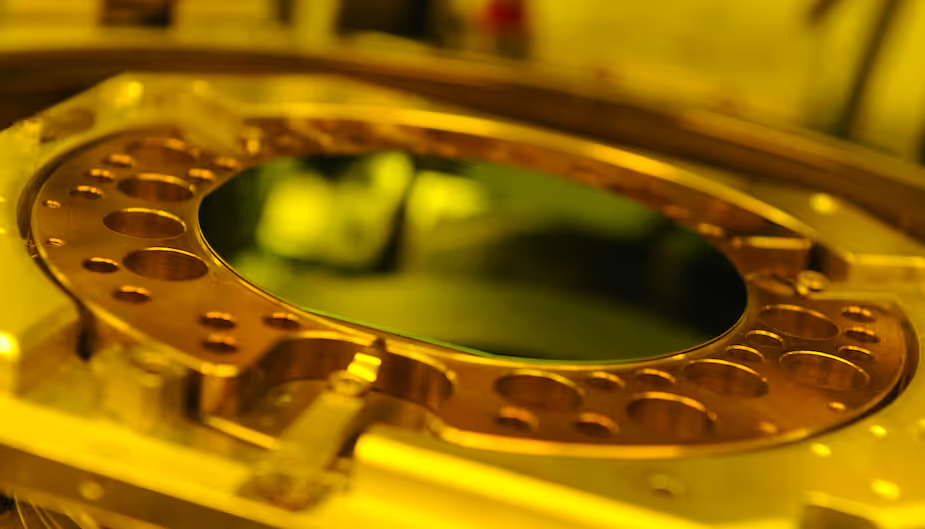
These have been fabricated in the clean room at TTP. To see the experimental results, you’ll need to tune in for part 2.
In conclusion, a wide range of variables can be exploited in optimising a MEMS mirror beam steering unit for the requirements of a particular lidar system. In our eyes, this is what makes the MEMS mirror solution “perfect”, making the design of other subunits less onerous. And when it comes to adoption, MEMS mirrors provide a scalable and low-cost solution.
TTP offers extensive experience in the development of low-cost sensors now also to the autonomous driving industry. Please contact us to learn more about our MEMS mirror design activity.