It’s not news that as we transition to renewable energy, we’ll have to learn to live with fluctuating power generation. From a technology perspective, the challenge that is gaining in importance is that on/off cycling or connection of a system to a variable power source can be very destructive in comparison to steady-state operation.
As we seek to buffer the energy we harness from renewables to balance supply and demand, we will be doing more of exactly that – for example by hooking up electrolysers and other power-to-X technologies directly to photovoltaic arrays or wind turbines with no grid connection to stabilise their power supply.
One example of this trend is the current interest in offshore hydrogen production powered by wind, with the energy being piped to shore in the form of gas. This can be lower cost than transmitting the energy as electricity, with the added advantage that the gas pipe itself can act as an energy buffer by allowing excess gas to increase the pressure.
But for commercial success, the electrolysers in such systems need to be very low capital cost to justify idle periods when the wind doesn’t blow. They would also need minimal maintenance and servicing, given their remote location.
Creators of power-to-X technologies need to address this question in order to access capital from investors who want to back them in tackling climate change but are balancing the benefits of the latest technology against the risk inherent in novelty.
In this post, I reflect on how intermittency resulting from fluctuating renewable power can be factored into lifetime and reliability considerations when developing power-to-X systems.
What do intermittency and dynamic operation mean for long-term reliability?
Intermittency means the system has some downtime, and downtime reduces wear. But it is also well-known that on/off cycling is hard on systems, often introducing fatigue cycles, surges in current, and other transition effects. Electrolysers and other power-to-X technologies are no exception.
This means that we’ll need to think about uncertainty in the lifetime of even standard components, while the lifetime of the key electrochemical components in these technologies is often less well understood, with many intricately related characteristics that challenge traditional strategies of accelerated life testing.
Designing systems to last the distance
When designing a complex system, we can normally take into account the lifetime of components. This can be visualised using a dendrogram, or tree diagram, where each branch represents a system component and its probability of failure. This information can help us to decide how to structure the system, what redundancy to build in, and how to design around the weakest links.
The red bubbles on the dendrogram show the unreliability accumulated on each branch from several components. So, bigger bubbles show branches where failures will occur with greater probability – providing us with a basis for designing systems with well-understood reliability.
But how will we manage this “tyranny of numbers” inherent in building any complex system if intermittent operation means that the lifetime of key components is uncertain?
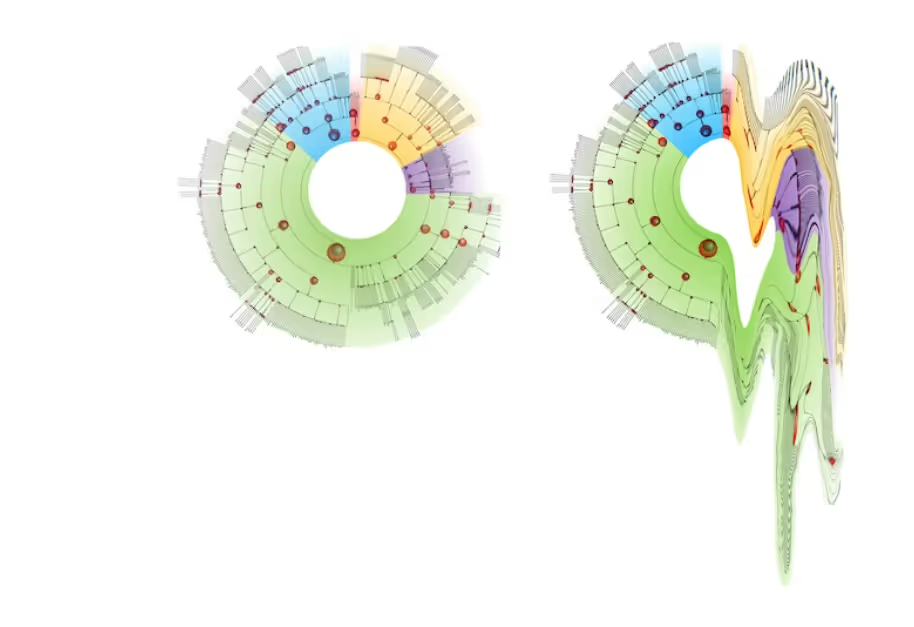
Manufacturers’ data typically gives the lifetime of components in a certain environment at constant temperature, but real-world operation can mean that the system will be cycling through conditions that wear the component out many times faster, over and over again.
One solution is to design the system such that the conditions that each component is exposed to are well aligned to those recommended by the manufacturer. A familiar example of this approach is to include a battery in a power-to-X system to take over during lulls in supply from the wind or sun. But such a strategy is not always appropriate as it tends to increase system cost and complexity.
Adding to the challenge, in power-to-X technologies the lifetimes of key components such as membranes or protective coatings on critical parts are often unproven. And the relationship between lifetime determined by accelerated lifetime testing strategies and real-world operating conditions may not be clearly understood.
We can, however, build up a scientific picture of the degradation mechanisms, which will help us to understand the durability of parts with a lifetime that is too long for conventional testing. And we can bring in a combination of modelling and testing to quantify sensitivity of lifetime to various operating conditions and infer what these relationships mean for operation in the real world.
Last but not least, we can build the system to use self-monitoring to reduce the consequential cost of failures. Sensor information can feed into a digital twin that warns the operator of impending failures. Sensing is complimentary to the above approaches to understand reliability, which will give us clues about what the sensors need to monitor.
Is it worth it?
The top priority for a new technology is often to demonstrate functionality at scale and in real-world conditions. The emphasis at this stage is on proving that the benefits of the technology (for example, lower operating cost, lower capital costs, or to suitability for intermittent operation) are sufficient to justify the increased risk of investing in equipment that is less mature than the incumbent solution.
The next hurdle is always to demonstrate that an investment in the new technology will pay back. This phase of development often requires the system design to be stripped back to its fundamentals and reassessed to make sure that it can last the course and won’t require costly unexpected interventions.
Charles Cooke is Sustainable Energy Lead at TTP. His agile team of scientists and engineers has solved a range of complex reliability engineering challenges. The team offers a combination of system design and scientific analysis to support the development of reliable and durable power-to-X technologies.
TTP has also developed SonicSense, a novel gas-sensing platform that can be adapted to meet the needs of a wide range of process monitoring and safety applications in the hydrogen economy.